Integrated management is supported by digital, real-time workflows with third-party QSE Accreditation. This transforms how we work.
At AnewX, we’re always implementing new ways of developing our employees, managing our equipment fleet, and using low cost cloud based systems to support the whole project life cycle—all in the name of creating greater effectiveness and efficiencies for our clients.
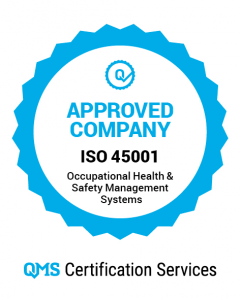
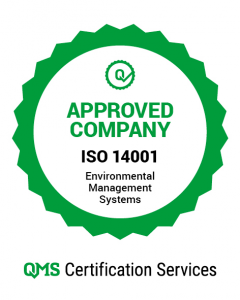
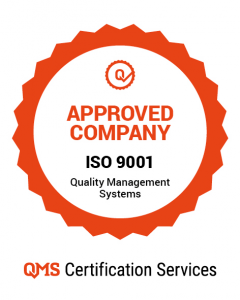
Since it’s inception in 2017, AnewX has managed all aspects of its business through a third party accredited IMS (Integrated Management System) for Health, Safety, Environment and Quality. The IMS is accredited to the following Australian Standards: ISO 45001: 2018, ISO 14001: 2015 and ISO 9001: 2015. We have now moved to interactive and real-time digital operating systems to support our fieldwork teams using Safety Culture & Track Unit technology.
Sustainability Goals
Our future in our hands—as we continue to work collaboratively with our Clients and suppliers to contribute to the United Nation’s Sustainable Development Goals. We’re committed to minimising the environmental and community impact of our activities, increasing the diversity of our workforce and supporting local Indigenous businesses.
- Educating our workforce with Indigenous cultural awareness training and supporting Indigenous owned construction suppliers
- Our foundation machines are modern, low emission and carry the latest engine management systems to optimise fuel consumption and consequently minimise emissions
- Biodegradable Panolin hydraulic oil is installed in all our foundation machines, providing positive reduction in emissions and greatly reduced impact from any hydraulic spills
- We’re always challenging solutions to minimise concrete usage and classify and recycle materials where possible
- Work experience placements and mentoring for the next generation of engineers, including sponsorship of Engineers Australia programs to attract more women into construction.
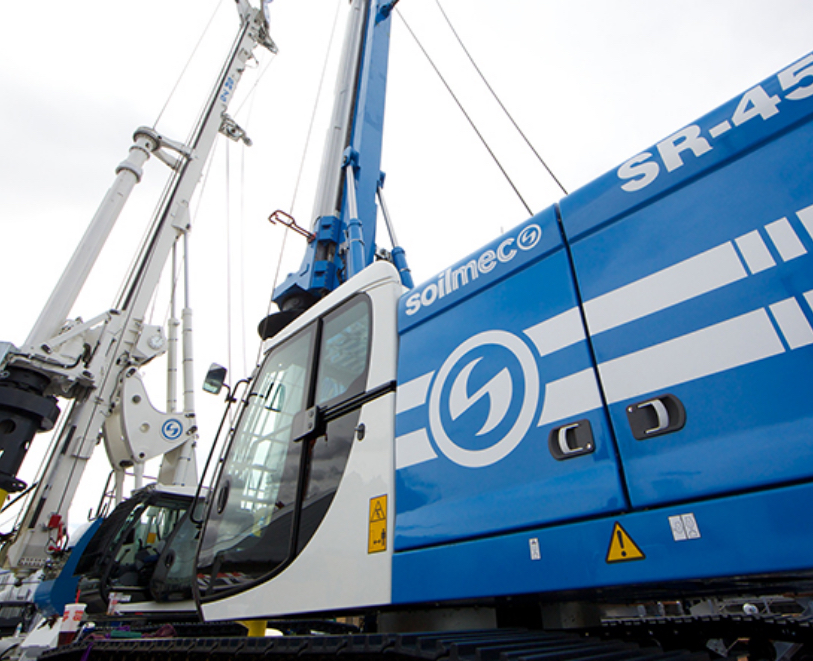
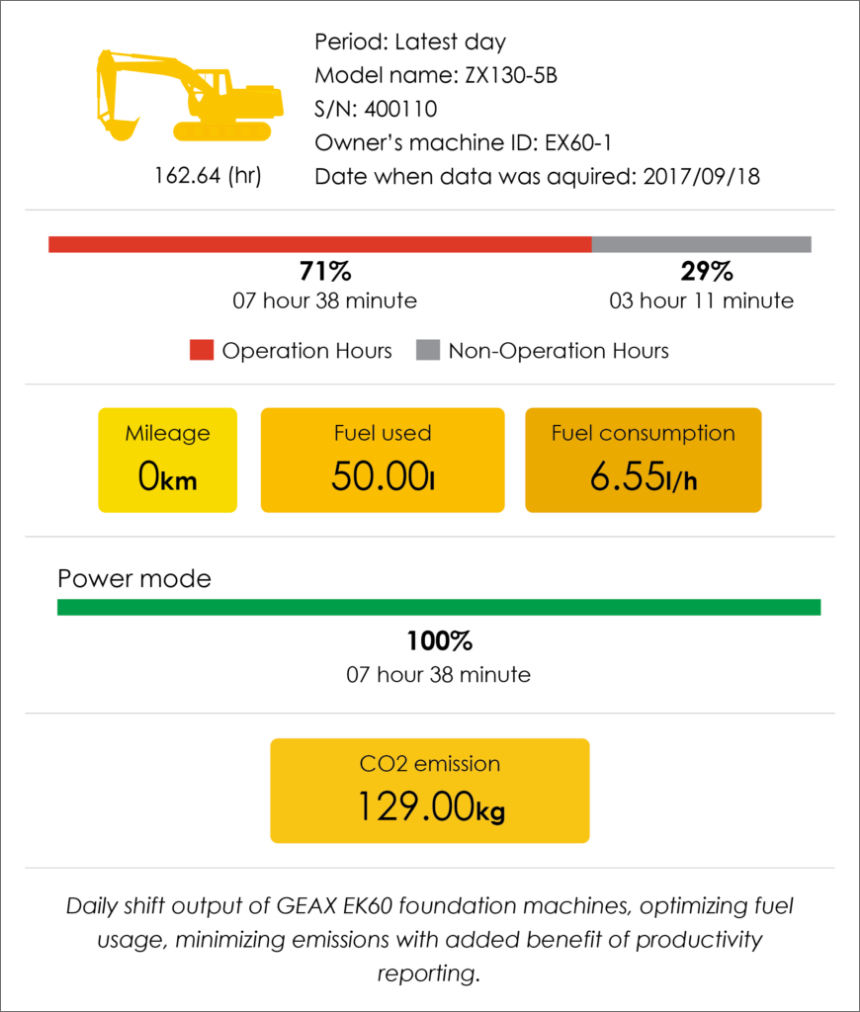


AnewX & ComplyFlow Digital
AnewX has formed a partnership with Comply Flow to deliver end-to-end software solutions for compliance management and supply chain assurance. The cloud-based system provides visibility and control to the AnewX management of complex operations, simplifying supplier engagement, pre qualification and compliance processes across the entire risk lifecycle.
From our smart phone, site based operatives we are able to manage in real time:
- Workforce management, including currency of competencies and training
- Plant inspections and management of maintenance
- Subcontractor management and compliance on our Projects
- Workplace inspections, and equipment compliance control
The use of this evolving technology has:
- Lowered the cost of our operation
- Increased the ability for our site based teams to manage their compliance
- Improved the effectiveness of our subcontractor management chain.